Blog
How do mining companies measure their success?
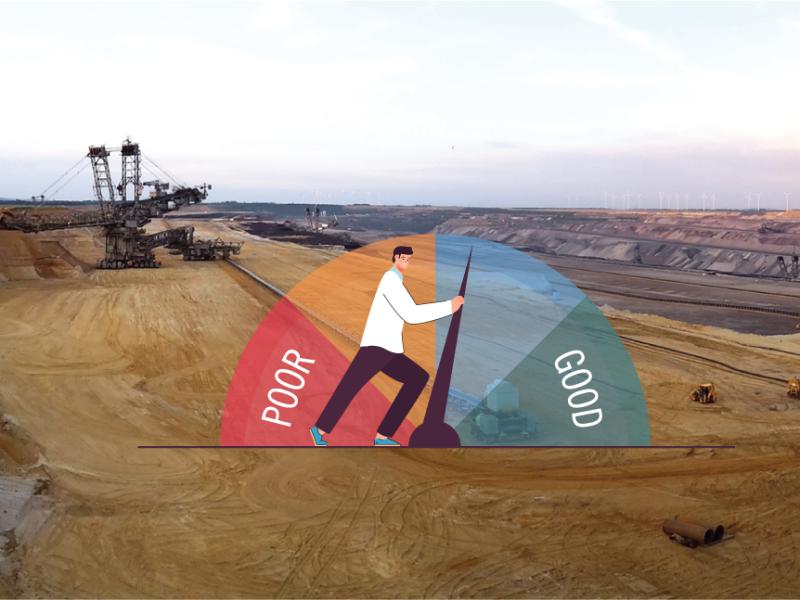
THE MEASURE OF A MINE
How do mining companies measure their success?
We all remember a time when profit was the only metric that mattered. Investors were willing to overlook questionable safety and environmental track records if the mines managed to make money. Investors no longer have an appetite for companies that make money at the expense of the environment, ethics, or people. Smart money is turning into green money, and mines that don't measure well against changing performance metrics will find themselves out in the cold. A question we often get is how to balance profitability against the demands of green-money investors.
Green Mines are Built on Sustainability
We have long maintained that this day is coming, and it is finally here. As prudent engineers, we have been working tirelessly to find solutions to this problem. We are proud to reveal that process intelligence tools are not just finding a balance between profit and environment. But that the efficiencies that digital technologies are unlocking, result in the pursuit of sustainability becoming one of the main drivers of profitability. As leaders in the mining industry are starting to redefine their business objectives into greater alignment with the principles of sustainability, many of them are realising that digital is the only way to achieve such lofty goals.
The answer is digital!!
4Sight's OT division and our technology partners have been working on solving these problems for mines through advanced digital solutions. Our products and services enable us to focus on the point of convergence where 4IR technologies like the IIoT, AI, and Machine Learning are helping mines to increase profitability as a direct result of their increases in sustainability. Digital technologies are powerful enablers that can evaluate multiple variables against historical and current performance parameters. Advanced analysis is then used to optimise the entire operation toward carbon neutrality by reducing energy and waste while simultaneously increasing safety and output.
Being Responsible
Since mining is the primary supplier of raw materials to the manufacturing industry, it finds itself a pivotal role player in the production of green products. Yet, mining, by its very nature, is very difficult to optimise. Consider the widespread geographical nature of mines, the various role players and the complexity of measuring and controlling inputs and process efficiencies. It's difficult to get your head around such an organic and complex structure. What is even more difficult, is filtering the lofty ideals of CEOs all the way down the pit, where human sweat and physical labour is often required to extract raw materials.
...but what about people?
But how does this impact your workforce? With the fear of humans being
replaced by machines waylaid, for now, process owners are realising the potential for greatness that results from a technology-empowered workforce. Digital decision-making tools are opening up insight into previously poorly understood process faults, enabling root cause analysis and breakdown prevention at historically unobtainable levels.
Mines that are training their operators and maintenance staff in using digital tools to make better decisions are already reaping benefits.
Insights into processes include:
- The ability to move from reactive maintenance to proactive maintenance and thereby greatly reducing downtime while increasing safety
- A better understanding of how every action impact profit
- Creating scalable solutions through open connectivity and access to data
- Create shorter ROI timespans and thereby increase lifetime profitability
- Become specialists in understanding operational trends and predicting and rectifying process anomalies.
Digital Momentum
Artificial Intelligence-based process solutions require the ability to gather industrial data quickly and accurately. When the solutions derived from digital intelligence are fed back into the system, it has a compounding flywheel effect. This results in increased momentum where staff and operational personnel implement predictive maintenance and other increases in efficiency at an ever-increasing speed. This momentum results in motivating staff as they can see their progress in real time to measure how their successes are impacting business results, improving profitability, optimising value chains, and increasing safety.