Blog
Laying the Groundwork for a Self-Optimizing Plant
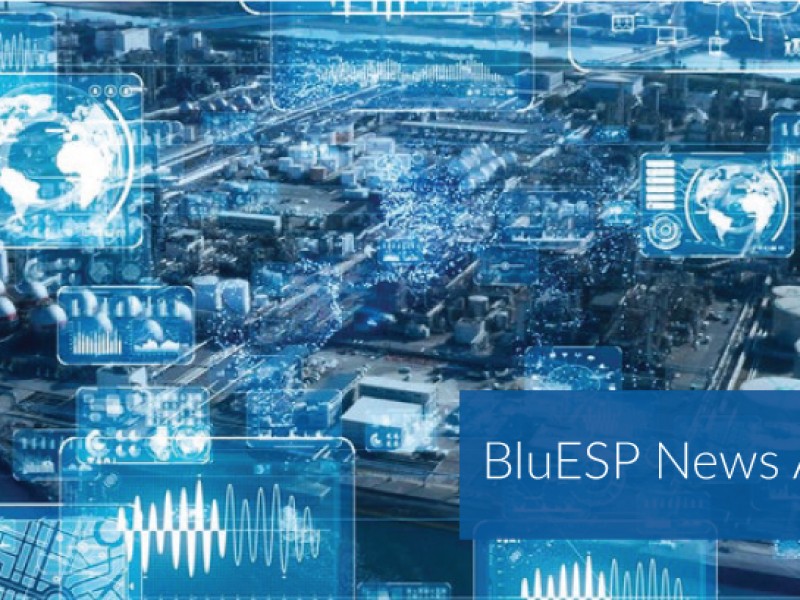
In manufacturing the focus is often on decreasing downtime and increasing productivity. But there are other elements that influence operations—including safety, reliability, and environmental impact. It’s clear that technology can help, especially artificial intelligence (AI) and analytics which can optimize processes and predict disruptions.
But not all AI is created equal. Aspen Technology (AspenTech), a maker of asset optimization software for process industries, recently released a new version of its aspenOne software that embeds its own Industrial-Strength AI across the portfolio. This is not your standard AI, company officials said, as it is not only about the algorithms, but also embedding domain expertise to contextualize AI so that it is specific to the industry, thereby creating insights and knowledge that adds value and can even transform the business.
It’s what the company calls Aspen Hybrid Models, which are part of the new aspenOne V12 software release, that applies data science, data cleansing, machine learning, and predictive insight into complicated processes.
“We are taking decades of domain expertise and embedding AI into that,” said Laura Rokohl, AspenTech’s senior director of product marketing. “We believe this helps advance our customers’ digitalization journey, but in terms of our vision as company, it’s this journey to the self-optimizing plant where things are moving toward autonomy and a closed loop. It’s a longer term multi-year journey but we feel this release helps us take initial steps toward the self-optimizing plant by embedding AI, automating things that were previously manual processes or required human intervention, and lowering the barrier to solve complex problems with less expertise.”
For example, mining plant data collected over years would previously require a controls expert to build the advanced process control (APC) model and it would take a few weeks to complete. With the embedded AI, the model-building process is shortcut. “It takes historical data, mines it, and creates a seed model. We refer to it as expertise-in-a-box. It dramatically reduces the time it takes to build that model as many of the steps are automated and packaged up,” Rokohl said, noting that while it doesn’t eliminate humans from the equation, it also doesn’t require 30 years of APC expertise.
According to Peter Reynolds, a senior analyst, ARC Advisory Group, “AI has the potential to enhance many industrial work processes, however, most companies are not well-equipped to bolt on AI themselves. While other technology strategies require asset owners to invest in complex platforms and data scientists, with embedded AI, users can get started right away improving margins and profitability.”
And that is the first step to the self-optimizing plant.
AspenTech defines the self-optimizing plant as a facility that can automatically respond to changing operation conditions. The company is now rolling out technology that delivers this next-generation of production optimization, including planning and scheduling, performance management, and adaptive process control that can continuously improve plant processes related to equipment wear, upgrades, feedstock quality changes, and fluctuating economic models. To that end, the aspenOne V12 release includes several new functions that can be added to the company’s existing product portfolio, thereby democratizing the application of Industrial-Strength AI.
AspenTech is also going beyond its core industry segments of energy and chemicals and branching out into metals and mining and food and beverage by including in V12 some functionality relevant to those industry, like its MES Collaborative application. MES Collaborative is an enterprise historian that sits in the cloud and can securely access data from sensors, PLCs, or an existing historian, for example, to pull more information into the enterprise view.
New Features of aspenOne V12 software include:
- Aspen Maestro – new capability for Aspen DMC3 and Aspen Mtell which automates the development of models faster by guiding a less experienced user on how to build a particular model or agent.
- Aspen Deep-Learning IQ – enables the building of more accurate models and predictions.
- Aspen Verify for Planning – uses AI to capture knowledge and check against plan to prevent costly mistakes.
- Aspen Multi-Case – easily runs thousands of simulations cases concurrently, on-premise or in the cloud, allowing a more complete analysis so results can be used to navigate operational complexity and make more accurate decisions faster.
- Aspen Event Analytics – provides rapid insight into production events. Fast, easy investigation of unexpected production events accelerates corrective action decision-making. Monitors and detects real-time events to enable rapid early intervention.
- Aspen MES Collaborative – delivers the connected enterprise. Aggregates data with an enterprise-level historian and connects small sites to eliminate stranded data.
- Aspen Cloud Connect – provides flexible connectivity with high performance and security to transfer data from edge to cloud.
- Aspen Capital Cost Estimator Insights (ACCE) – streamlines the user experience with out-of-the-box integration with ACCE and Aspen Enterprise Insights to provide visualization and collaborative workflow within a hybrid cloud environment.
Ultimately, AspenTech recognizes that the way plants work will have to change in the future, and they are laying the groundwork for that paradigm shift.
“The process industries and other capital-intensive industries are experiencing new levels of volatility in supply and demand, and the need to be agile in response to all market conditions requires a new approach to asset optimization,” said AspenTech president and CEO Antonio Pietri. “This next generation of Industrial AI solutions will change how process industries work.”