Blog
Maintenance and Reliability Managers: Make Your Assets More Reliable
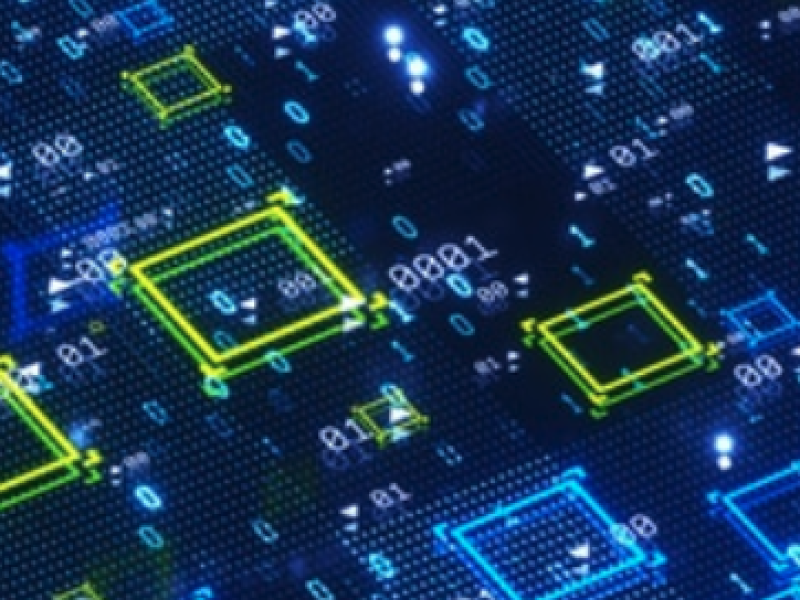
Sr. Product Marketing Manager, APM, Aspen Technology, Inc.
What does a day in the life of maintenance and reliability managers look like? What are their priorities? Are they focused on the highest value issues for the plant or are they bogged down by daily issues? While no two plants are identical, day-to-day activities in reliability and maintenance across manufacturing generally include:
- Identification and diagnosis of any issues highlighted by Operations or Health, Safety and Environment (HSE) teams
- Collaboration with planners, schedulers and operations to develop daily/weekly job plans
- Driving application of consistent processes across craft teams and technicians
- Monitoring KPIs to ensure success in planning, reviewing and closing out work orders while meeting maintenance schedules, reducing rework within budgets
Our experience suggests Maintenance and Reliability teams generally spend most of their time managing day-to-day issues at the cost of attention to root cause analysis of bad actors. This is due to both a lack of reliability strategy across many industry participants and a lack of high-quality tools which can support reliability improvement efforts. For example, a wide variety of methods are used to detect signs of equipment failure, but these are late-stage indicators, which often do not provide sufficient advance warning to allow mitigating actions to be developed and deployed.
How do AspenTech Solutions Aid Maintenance and Reliability Teams?
Thanks to advances in artificial intelligence, automation and data, maintenance and reliability managers are turning to new technologies to increase reliability and availability of assets. Prescriptive Maintenance Solutions predict failures early by analysing time series data to identify fingerprints of known failure or anomalous behaviour. Such solutions recognise subtle changes in operating parameters and provide leading indicators of asset degradation. These solutions are also able to prescribe preventative actions based on prior experience in similar situations for the same asset or from other assets in the system. Implementing prescriptive maintenance solutions that provide advance warning and mitigation recommendations can be of great help to maintenance and reliability teams.
Accelerate Implementation Times
Machine Learning (ML)-based solutions analyze sensor data to recognise deviations from normal behaviour – this is accomplished by software elements known as Agents. Maintenance teams can now deploy Agents across a unit or a site faster than ever with the help of asset templates. Asset templates include step-by-step instructions to map sensors to predefined sensor roles provided in the template to build Agents. In our experience, maintenance teams can develop and deploy agents with limited support, typically within days of onboarding the maintenance solution and undergoing the required training. Deploying Agents allows maintenance teams to reduce troubleshooting time on a daily basis and frees up time to focus on high ROI activities.
Provide a Consistent Framework to Address Maintenance and Reliability Issues
Troubleshooting is the first step when an equipment issue arises. This step can be time-consuming if personnel addressing the issue are not familiar with the asset or do not have sufficient experience in similar situations. Smarter maintenance solutions notify teams of specific sensors contributing to the issue and leverage in-built reliability engineering methods such as FMEA (Failure Mode and Effects Analysis) to highlight potential mitigating actions. In instances where a “never-before-seen” issue arises, the solution allows personnel to document the learnings for future use. By following this consistent approach, maintenance teams can effectively reduce future risks and improve asset availability by reducing maintenance time.
Help Prioritise and Manage Maintenance Tasks Based on Inherent Risk
While advance warning of issues is beneficial, a prioritised response to these alerts is equally important. A centralised asset health interface enables maintenance teams to make decisions effectively by prioritising alerts and scheduling preventative work, considering personnel and spare parts availability. A prescriptive maintenance solution that allows alerts to be sorted by criticality, severity and urgency, provides a higher level of visibility for maintenance teams. to develop and manage schedules in collaboration with operations, planners and schedulers. An end-to-end prescriptive maintenance solution should provide a single-point approach and a structured method to review, prioritise, schedule and track maintenance work orders.
Learn More from AspenTech at IMC
At AspenTech, we are constantly innovating and improving our industry leading prescriptive maintenance solution for users across all levels of an organisation to take advantage of advanced analytics.