Blog
Unleashing the power of Generative AI in industry
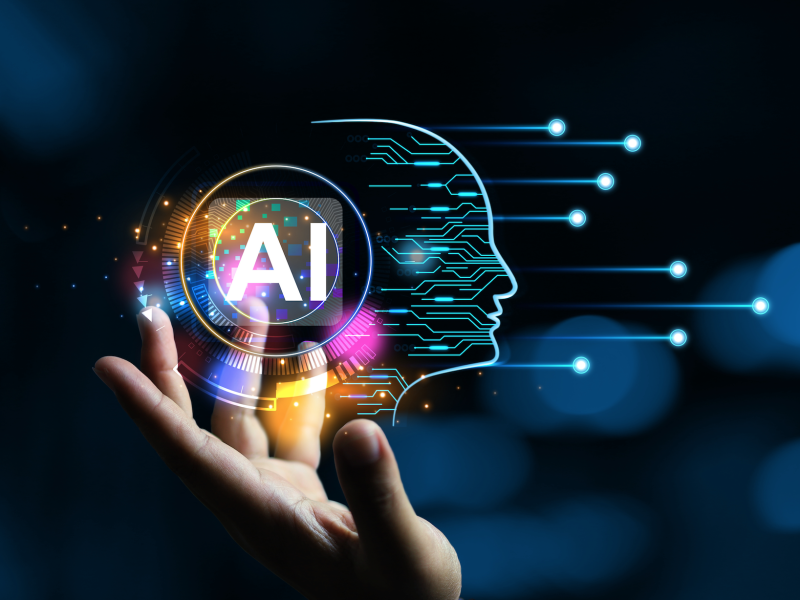
In the rapidly evolving landscape of Industry 4.0, generative AI stands out as a transformative force poised to revolutionise industrial operations. From optimising manufacturing processes to enhancing predictive maintenance, generative AI’s potential applications are vast and far-reaching. At 4Sight Operational Technologies, we are at the forefront of integrating these cutting-edge technologies to empower businesses with unprecedented efficiency and innovation.
Transforming Manufacturing Processes
One of the most significant impacts of generative AI is in the realm of manufacturing. Traditional manufacturing methods often rely on static designs and fixed processes. Generative AI, however, introduces a dynamic approach where algorithms can create thousands of design iterations based on specific parameters and constraints. This capability enables manufacturers to explore innovative designs, optimising material usage, cost, and performance, leading to more efficient production processes. For instance, generative AI can help design lighter yet stronger components, reducing material costs and energy consumption during production.
Moreover, generative AI can facilitate the shift towards more sustainable manufacturing. AI-driven design processes contribute to greener production methods by optimising material usage and minimising waste. Companies can achieve their sustainability goals while enjoying cost savings, thus aligning economic and environmental benefits.
Enhancing Predictive Maintenance
Predictive maintenance is another area where generative AI is making a substantial difference. By analysing vast amounts of data from sensors and equipment, AI can predict potential failures before they occur, allowing for timely maintenance and reducing downtime. This proactive approach enhances equipment longevity and significantly cuts maintenance costs, providing a competitive edge in operational efficiency. For example, an AI system can detect subtle changes in vibration or temperature that might indicate a looming failure, enabling technicians to address issues before they escalate. Integrating generative AI in predictive maintenance also facilitates the creation of intelligent maintenance schedules. By continuously learning from new data, these systems can adapt and refine maintenance plans, ensuring equipment operates at peak efficiency with minimal intervention. This continuous learning capability makes generative AI a powerful tool for maintaining optimal industrial operations.
Revolutionising Supply Chain Management
The supply chain is the lifeblood of industrial operations, and generative AI transforms how it is managed. AI algorithms can analyse historical data and market trends to predict demand, optimise inventory levels, and streamline logistics. This precision ensures that companies can meet customer demands promptly while minimising excess inventory and reducing operational costs. For instance, generative AI can help forecast seasonal demand fluctuations, allowing companies to adjust their inventory and production schedules accordingly.
Generative AI enhances supply chain resilience by identifying potential disruptions and suggesting alternative strategies. By simulating various scenarios, AI can help companies prepare for unforeseen events such as natural disasters, geopolitical tensions, or sudden market shifts. This predictive capability ensures that businesses maintain continuity and mitigate risks in their supply chain operations.
Driving Innovation with Digital Twins
Digital twins, virtual replicas of physical assets, are becoming increasingly sophisticated with the integration of generative AI. These digital counterparts allow for real-time monitoring and simulation of industrial processes, providing invaluable insights into performance and potential issues. Generative AI enhances digital twins by enabling them to simulate countless scenarios, predict outcomes, and suggest optimal solutions, driving continuous improvement and innovation. In practical terms, a digital twin of a manufacturing plant could simulate the impact of a new production line configuration before any physical changes are made. This capability reduces the risk and cost of trial-and-error approaches in physical settings. Additionally, digital twins can aid in training new employees by providing a risk-free environment in which to explore and understand complex industrial systems.
Click here to schedule a meeting with Wilhelm Swart