Case Studies
Success Case - Bridgestone VIC Mixer - Control System Upgrade
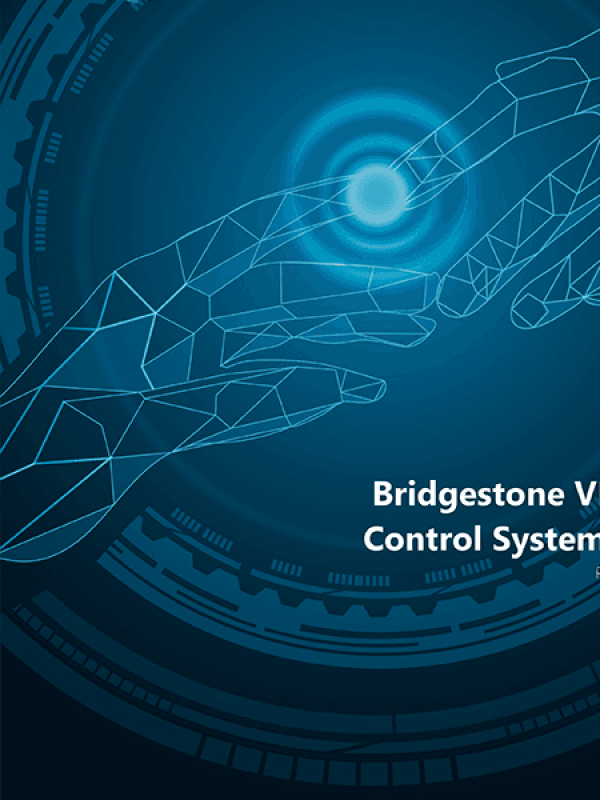
The VIC Mixer provides unique, additional processing parameters of special importance for the Bridgestone Mixer family – it allows for the gap between rotors to be adjusted during the mixing process and for precision temperature control. This makes it a unique Mixer for Bridgestone’s arsenal of Mixers, and a vital part of their manufacturing process.
Business Needs and Challenges
The VIC Mixer upgrade project posed a few challenges to overcome, in order to meet the company's business and process needs:
- Performance of the mixer needed to be improved, to achieve higher levels of production and improved quality of the rubber
- The project needed to stay within the budget allowance for the upgrade.
- 4Sight AGE needed to ensure that the regulation and compliance to business and safety standards were
- The upgrade needed to be completed within a 12 month
- The entire Mixer upgrade came from different parts of the world (Italy, Germany, China and South Africa), all of these Technologies had to be integrated into the overall Batch control of the VIC Mixer.
Project Requirements
New Batching Software written for the VIC Mixer for Raw Rubber and Pigment weighing as well as automated Carbon Black feeding system from Twelve Different Types of Material Bins, VIC Mixer Pressure Control on Hydraulic RAM, Temperature Control inside the Mixer, Gap Control between the Rotors and to integrate all Vendor Control Systems for Harmony- and Silane Oil dosing, Mixer Hydraulics, Convex System and Automated Batch off System.
The 4Sight AGE Solution
4Sight AGE implemented Rockwell Automation’s GuardLogix PLC with a focus on Operator safety complying with IEC61508 standards. Features and benefits of the system include:
- Variable distance between rotors for optimal process steps
- Fast intake and adjustable shear level
- Flexibility for different process applications
- Durable crack-free hard facing for an extended lifetime
- Hydraulic ram with highly accurate pressure control
- Hydraulic dust seals with multiple cylinder concept (HCD) for superior sealing and easy maintenance
Advantages of the upgraded VIC Mixer system
Advantages of the upgraded mixer system include - The new VIC Mixer allows Bridgestone SA to produce different types of compounds than the current Mixers. The Optimal Temperature Control feature allows for temperature-sensitive compounds, such as silica, to also be manufactured. The flexibility and versatility of the system allows for application in different processes, improving efficiency in the manufacturing process.
Benefits for the company and processes
The VIC Mixer offers several benefits for Bridgestone SA:
- Allows for the very fast intake of raw materials into the mixing chamber
- Increases the quality of rubber dispersion
- Delivers high specific energy into the compound in the shortest amount of time
- Control’s temperature optimally
In Conclusion
Mixing affects the whole process of rubber production and its results, which is why it is a vital part of the production process, and the need arises for efficient and high-performance systems. The VIC Mixer upgrade allows Bridgestone SA to produce more high-quality amounts of rubber in less time.