Case Studies
Enhancing Power Generation at Kibali Gold Mine with Mtell Asset Performance Management
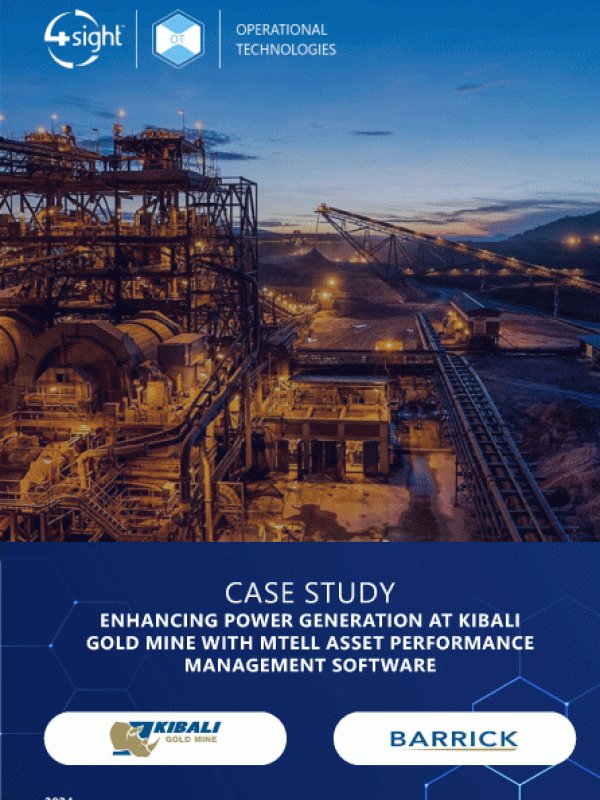
CUSTOMER SUMMARY
Kibali Gold Mine, located in the Democratic Republic of the Congo, is the largest gold mine in Africa. It is a joint venture between Barrick Gold Corporation and AngloGold Ashanti. The mine produces significant quantities of gold and generates its own power to ensure continuous operations. Ensuring the reliability and efficiency of the power generation plants is critical to the mine’s success. Kibali Gold Mine reached out to 4Sight, which has implemented the AspenTech Mtell Asset Performance Management (APM) solution. Kibali Gold Mine operates in a challenging environment where reliable power generation is crucial for maintaining continuous mining operations. The power generation plants at Kibali include multiple diesel generators and hydropower units. Ensuring these assets operate efficiently and without unexpected downtime is essential for the mine’s productivity and profitability.
Challenges
The mine engaged 4Sight to explore how data from its existing sensor network could be leveraged to enhance detection capabilities, enabling proactive corrective actions that ultimately improve the availability of the power units:
- Preventing Unplanned Downtime: It is crucial to assess the consequences of failures that could lead to operational disruptions.
- Ensuring all sensors remain functional: One of the key challenges is ensuring that all sensors remain functional and in optimal condition. Providing proactive monitoring and predictive insights to maintain sensor health and reliability.
Solution
To address these challenges, Kibali Gold Mine implemented Mtell APM software, a predictive maintenance solution by AspenTech designed to monitor the performance of critical assets. Data from the existing sensor network is processed by using advanced machine learning algorithms and big data analytics to detect anomalies that deviate from normal operating conditions. These deviations can be associated with faulty sensors or potential equipment failures, allowing the maintenance teams to further investigate and rectify the potential problem.
Implementation
The implementation process of Mtell APM at Kibali Gold Mine involved several key steps:
- Data Integration: Mtell was integrated with the existing data infrastructure, including sensors and control systems, to collect real-time data from the power generation equipment.
- Model Training: Machine learning models were trained using historical and real time data to predict deviations from normal operating conditions. These deviations can be associated with faulty sensors or potential failure conditions.
- Adding Agents: The end user continuously needs to add “agents” to the system to detect anomalies to improve the accuracy.
- What Mtell is doing: Currently Mtell is checking for any deviations from normal operating conditions. Corrective tasks can be scheduled based on inspections performed after a notification was received from Mtell, should a deviation exist.
Results
Since the implementation of Mtell APM software, Kibali Gold Mine has experienced several notable benefits:
- Avoided Downtime: The predictive capabilities and monitoring of sensors in Mtell have aided in detecting potential failures for the power generation equipment, ensuring continuous power supply to the mining operations.
- Cost Savings: Through the monitoring of online sensors of the equipment, the maintenance team had time to plan and allocate resources and spares in order to prevent the equipment from downtime.
- Prescriptive Maintenance: Through comments on alerts and corrective actions saved, the maintenance team
is developing their prescriptive maintenance strategy and aiding in over all Reliability Root cause analysis by analysing the history accumulated on Mtell. - Enhanced decision making: The extra layer of protection and new insights while working with Mtell empowered the team to make better decisions and to detect fault conditions on sensors and assets at an early stage. The faulty sensor detection capability improved the fault detection capability.
Conclusion
Alongside the good maintenance practices already being implemented at Kibali, Mtell adds the added protection and prediction towards enhancing asset reliability. With guided inspections from the Mtell alerts and adoption into their maintenance strategy, Kibali continues to improve in their maintenance agenda. With further usage, improvement, and upkeep, the maintenance team will continue to avoid unexpected failures, over all reducing their maintenance costs, and move towards prescriptive maintenance. The success of this implementation highlights the critical role of advanced asset performance management solutions in ensuring the continuous and reliable operation of critical infrastructure in challenging environments.