Case Studies
Success Case - Resolution Copper: The benefits of pre-feasibility phase insights
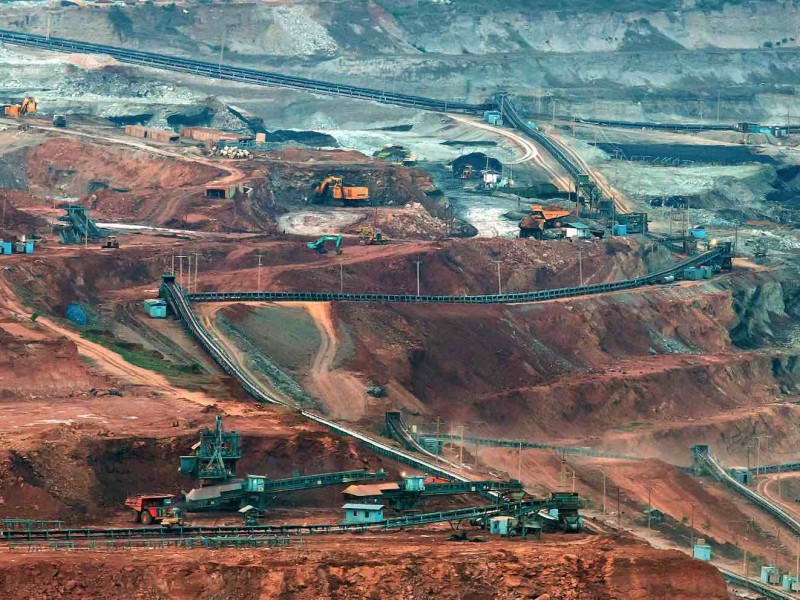
INTRODUCTION
As part of a pre-feasibility phase, one of North America’s largest proposed underground copper mines, ‘Resolution Copper’ required a simulation solution to evaluate the mine’s planned development, ramp-up (to steady-state) and production capacity. The implemented mining method is Blast Hole Stopping (BHS), and the simulation study needed to determine the mobile and fixed equipment configuration needed to develop and mine the planned production levels and transport the rock to the surface. The SimMine simulation software was used and is ideal for the requirements and objectives of this study.
APPROACH
SimMine was used to create a detailed simulation model from the mine designs. These included rock densities, face size properties, stope blocks and volume & paste fill attributes, among others. Detailed mining activity cycles, infrastructure characteristics (e.g. muck bays, tunnels, ramps, etc.), dependencies and supporting activities (e.g. bolting, shotcreting, etc.) were configured. As part of evaluating multiple scenarios, crews, schedules, equipment, material handling and availability parameters were considered in various combinations and configurations.
SOLUTION
The simulation study assisted the customer to:
• Evaluate and compare various development options for the underground infrastructure
• Estimate the production capacity of the ore handling system, including interference between unit operations.
• Verify if the underground mining system as a whole can meet the production schedule when the simultaneous interaction of the unit operations related to the mining method is considered.
• Verify if the backfill system capacity is not a constraint for mine output when multiple stopes are either in production or preparation.
• Quantify and verify the potential opportunities technology can bring to this project regarding upside productivity and associated energy and environmental benefits.
OUTCOME
Initial results indicated that operating parameters for certain equipment, such as velocity, loading/tipping times, drill philosophy and pastefill curing time, had to be reviewed and optimised in order to achieve the envisaged production ramp-up.
The simulation study concluded that the project was feasible to achieve the production targets for the development, ramp-up and steady-state production periods (10 years). Key results of various optimisation and sensitivity scenarios are as follows:
• Increased LHD size by 22%
• Decreased LHD fleet by 20%
• Determined the use of hollow tech bolters in development vs. standard resin bolts
◦ Reduce the required bolter fleet by 29% due to reduced cycle times
• Determined the use of ore pass loading shuts to further reduce the number of LHDs required for loading haul trucks
Further, it was found that bi-annual plant shutdowns significantly impact surface stockpile operations that impact mine production performance when the stockpile is 20kt or smaller). In order to address this issue, it was found that one additional haul truck would be able to add sufficient capacity to make up for production losses during plant shutdowns. Alternatively, it was found that if the surface stockpile is increased to 40kt, it would offer sufficient capacity not to constrain production during plant shutdowns.
Lastly, it was found that implementing a 10h shift time rather than a 12h shift time is infeasible as only 78% of the planned annual steady-state throughput could be achieved.