Blog - Operational Technologies
The benefits of predictive and prescriptive maintenance in mining autonomy.
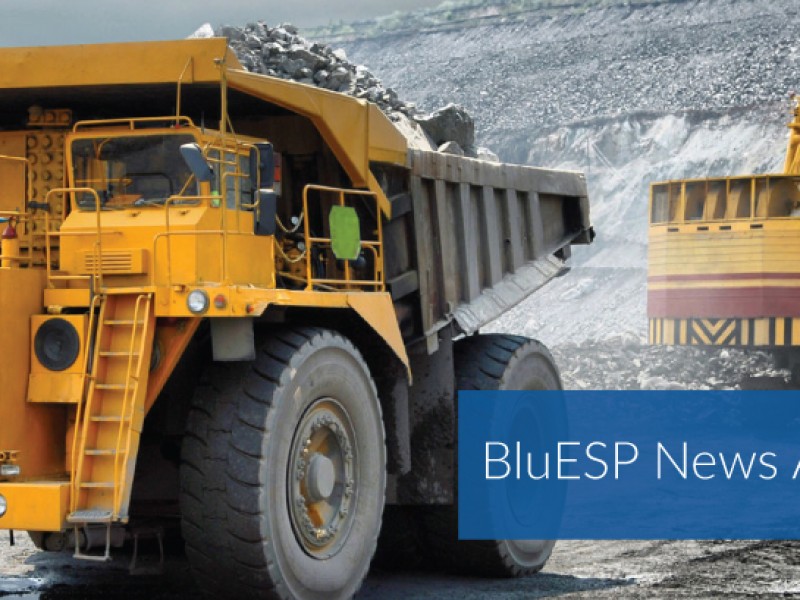
Optimised performance, reliability, availability and safety can be achieved with the automated operation.
Digitalisation in the mining industry is allowing mines to expand the utilisation of technologies being used successfully both at the mine and plant levels, one of the most significant of which is mine equipment autonomy.
While an exciting prospect, the mining industry is still having challenges as it works to integrate new technologies onto its mining equipment, such as shovels, drills, and trucks for capabilities like communications and positioning.
Consider, too, that just because a mine has become automated does not mean that maintenance pro-grams should be eliminated. On the contrary, they are perhaps more important than ever to support the optimised factors like avail-ability and utilisation of mine equipment – now auto-mated workings – as customers demand more than ever from their technology.
It is also key to remember that there are many layers to mining autonomy that must be consistently evaluated and monitored, from positioning to fleet cycle times, communications, incident reporting, safety reporting and infrastructure, such as conveyor lines.
“Aspen Tech’s deep process expertise and knowledge of the fundamental chemistry, equipment properties, and science – combined with new asset management capabilities – has enabled it to focus on asset lifecycle optimization,” said Peter Reynolds, contributing analyst for ARC Advisory Group1.
Within each subsystem exists the opportunity to excel, maintain status quo or to fail – and ensuring success, according to Aspen Technology, Inc., is centered within the application of predictive and prescriptive maintenance.
Aspen Technology, Inc., also known as Aspen Tech, has taken the lead on pushing digital transformation of the mining, chemical, engineering and oil/gas industries by optimising assets through the use of artificial intelligence (AI) within its leading-edge software that keeps mines safe, sustainable, and at their best operational levels.
Moreover, Aspen Tech’s focus on rapid time to value ensures return on investment in months, not years, facility wide scalability and continuous evolution; all using existing data and existing resources.
In business for more than three decades, Aspen Tech has the full-service expertise to perfectly weave its machine learning and AI technology into a customer’s plans and goals, helping translate the goal of autonomy into tangible action.
What is predictive maintenance? Prescriptive maintenance? What are the benefits of both?
On the other hand, prescriptive maintenance (RxM) takes things a step further to not only predict the potential issue, but also to offer information regarding potential causes before failure occurs. While the two terms are spokes of the same wheel, the latter’s goal is to provide recommendations that apply the anticipated outcome using analytics with greater lead time and cast a broader net on overall facility impacts and causes.
Much newer than PdM, RxM is quickly becoming part of best practice protocols at mining operations and other industrial work sites that Aspen Tech serves.
By definition, both maintenance types parallel the future of autonomy perfectly. There are two key benefits to autonomy in any industry – to improve safety and productivity – and PdM and RxM are built upon those same foundations.
For example, in an automated mining operation using predictive maintenance for its mobile equipment fleet, there may never be one moment when any employee is in the line of danger.
Because its maintenance program can identify the issue quickly, minimal downtime may be needed to rectify said problem before it even becomes an actual incident – and potentially this fix could be done right from a control room at the site (or even miles away at a remote center). This means higher availability and reliability, too, and of course a cost savings for the client.
Bringing it all together: Aspen Mtell®
For metals and mining, Aspen Mtell will change the maintenance game. A prescriptive maintenance solution marries the inherent, often muscle memory, knowledge of existing operations with existing pro-cess data to automatically alert when a failure could occur, potential causes, and the scope of that failure – earlier than ever.
With early detection, high accuracy with fewer false alarms, prescriptive maintenance and fast deployment times using low-touch machine learning, Aspen Mtell offers the capability for a customer to identify patterns in operating data that can predict degradation well in advance of it becoming reality. It uses leading edge technology including failure pattern recognition and model-based solutions to offer un-precedented accuracy. Such accuracy is paralleled when examining data for only a singular piece of equipment. By getting to the heart of the mine system, Aspen Mtell can easily calculate the lead time of an impending issue.
However, it can also reveal the ideal prescriptive guidance to mitigate a breakdown, or prevent it altogether. Cost improvements for operational continuity are indeed possible with Aspen Mtell, which offers low implementation costs and a rapid deployment turn-around.
In short, Aspen Mtell’s prescriptive maintenance software can reduce the time spent searching for root causes, as well as help it to perform longer, reduce an operation’s maintenance costs and even drive in-creased production.
The industrial sector has also taken notice; Singapore Business Review recently named the technology a winner in its 2020 Technology Excellence Award for AI Manufacturing, and Hydrocarbon Technology named Aspen Mtell Best Asset Monitoring Technology for 2019.
Operationally, Aspen Tech can point to its client successes as well, including a recent deployment of As-pen Mtell for the truck and shovels at a leading mining company’s open-pit copper mine.
Aspen Mtell is also a significant part of an overall industry shift from ‘calendar maintenance’ to prescriptive techniques that is ongoing. Big data is only big if it is useful, and AspenTech has the expertise to allow data to be effectively managed and utilised to achieve an ultimately outstanding outcome.
The future of digitisation: Aspen Tech’s take
Mines, well sites, engineering projects – no matter the industry, talk of ‘going digital’ is not new, nor will it soon end. In light of the COVID-19 pandemic, discus-sions of digital technology, automation and the need for operational continuity are more common and pervasive in most industries including mining.
The biggest opportunity of digitalisation and autonomy at this time is primarily tied to costs: reducing maintenance costs, ensuring ongoing operations, and improving operational metrics. The challenges, conversely, include centralising mobile equipment data in a common repository, as well as migration for a client from from preventive to predictive maintenance.
“Thanks to centralised monitoring… mine equipment can be efficiently managed by a proper fleet management system, utilising predictive and prescriptive maintenance to improve equipment availability and consequently improve the mine operational reliability,” according to Aspen Tech’s Eugenio Gomez. “An unexpected shutdown in any of the mine equipment will create a huge loss of productivity and consequently hundreds of thousand dollars for the business.”
Published in Mining Magazine: www.miningmagazine.com