Case Studies - Operational Technologies
Using digital-twin simulation to de-bottleneck Letšeng processing plant
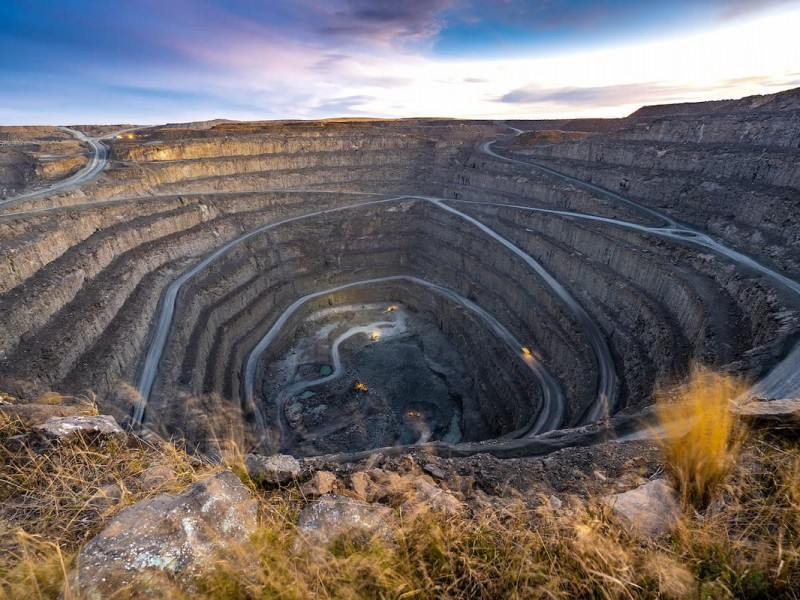
Customer Summary
The Letšeng diamond mine focuses on optimising expansion projects to reduce diamond damage, enhancing diamond protection, improving diamond liberation and recovery, and implementing optimised life of mine (LoM) extension solutions.
Three key objectives that underpin Gem Diamonds’ strategy:
- Extracting the highest value from operations,
- Working responsibly and maintaining its social license, and
- Preparing for the future through the advancement of innovative technologies.
Challenges
Letšeng wanted to increase production but needed a way to interpret the status quo and get greater visibility on the internal workings of the processing plants. They required a holistic view of the current operations and the results of specific scenario analysis to identify the optimal changes needed to maximise performance. Without the knowledge of how different variables were impacting the plants, Letšeng could not easily locate bottlenecks and were not in a position to make informed decisions on how to achieve optimal output.
“The project has fostered a collaborative working relationship with Minopex and 4Sight, combining expertise and experience across various industries and systems to take the business forward.”
- Jaco Houman, Senior manager – Technical and Projects
Solution
The partnership between Minopex© and 4Sight presented Letšeng with a unique service offering, combining Minopex’s© and 4Sight’s extensive expertise in multiple areas and an accomplished knowledge base and track record. With Minopex’s© vast understanding of complexities in mining operations and plant maintenance and 4Sight’s OT Cluster’s simulation capability, the team built a dynamic simulation model, using the empirical data as input to ensure an accurate replication of the plants. A baseline was established to ensure the model logic simulated the current plant performance. This simulation verified pre-defined hypotheses, with the outcomes being analysed and used to drive positive adjustments.
"We now have a common view of the constraints or bottlenecks to tackle to enhance performance”
- Jaco Houman, Senior manager – Technical and Projects
Benefits & Outcomes
A simulated environment helped the multi-disciplinary team to ascertain how to improve and optimise. The model assisted the team to identify
bottlenecks and test associated improvement initiatives such as:
- Finer Blasting, finer and coarser Particle Size Distributions (PSD)
- The potential impact of Advance Process Control (APC)
- Equipment Upgrade options
- Reduced Downtime through technologies like Asset Performance Management (APM)
- Flowsheet changes or reconfiguration of splits and mass balance to de-constrain the process
The evaluated scenarios resulted in decisions and actions based on factual information rather than assumptions, enabling complete debottlenecking, and focused and appropriate capital expenditure. In one month alone the project delivered a return on investment – Letšeng verified they increased the output by 10,000 tonnes, resulting in the additional revenue of $167,000. Ultimately, Letšeng received the benefit of understanding the overall performance and making insightful decisions to drive continuous improvement. The dynamic simulation model is currently being expanded to include the mining operations and offer a complete value chain solution.
In time, the model will form part of the planning processing, actively testing initiatives before they are implemented and predicting future performance, to give an achievable market forecast. Gem Diamonds, Minopex, and 4Sight are working together to integrate the model with live data sources, to create a true digital twin of the operations.