How Asset Automation Drives Cost Savings in Manufacturing
At 4Sight OT Automation, we are leaders in providing automation and control systems for various industrial needs. With extensive expertise in asset automation, we empower manufacturers to streamline operations, enhance productivity, and reduce operational expenses. Let’s dive into how asset automation can bring transformative cost savings to manufacturing processes.
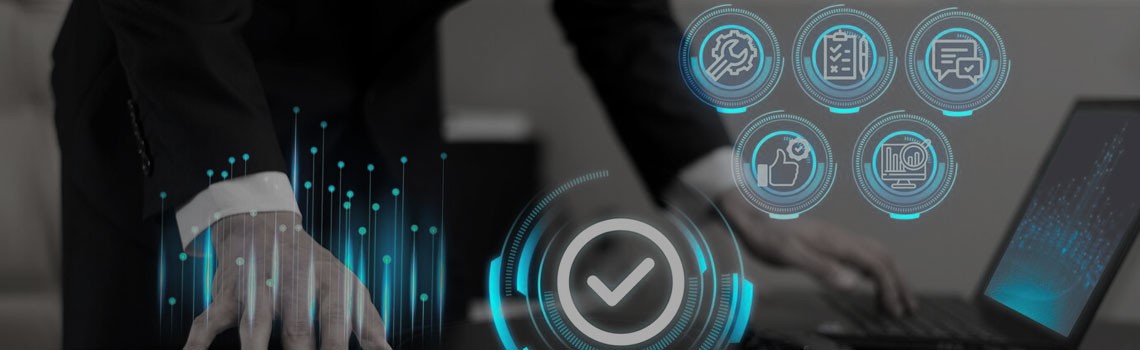
What is Asset Automation?
Asset automation refers to using advanced technology to manage, monitor, and optimise industrial assets throughout their lifecycle. By incorporating IoT integration, predictive maintenance, and real-time data collection, asset automation enhances operational efficiency, reduces downtime, and supports long-term cost savings.
For instance, integrating smart assets into manufacturing enables businesses to remotely monitor equipment, predict failures before they occur, and make data-driven decisions. This not only boosts productivity but also minimises costly disruptions in production.
The Role of Asset Automation in Manufacturing Cost Savings
1. Predictive Maintenance
One of the most significant benefits of asset automation is its ability to facilitate predictive maintenance. Traditional maintenance models often rely on scheduled servicing, which can lead to unnecessary costs or unexpected breakdowns. With predictive tools powered by real-time monitoring systems, manufacturers can:
- Detect potential failures early.
- Reduce unplanned downtime.
- Prolong the lifespan of critical equipment.
This proactive approach lowers repair costs while ensuring consistent production output.
2. Enhanced Operational Efficiency
By automating repetitive tasks and optimising workflows, manufacturers can achieve greater operational efficiency. Asset automation solutions such as SCADA systems and PLC programming enable seamless integration of machines, systems, and processes. This ensures:
- Reduced manual intervention.
- Faster production cycles.
- Improved accuracy in operations.
Learn more about how automation improves industrial performance with our guide on quality control in process automation systems.
3. Real-Time Data Collection and Analytics
Data is invaluable in manufacturing. Asset automation systems collect and analyse real-time data to identify bottlenecks, inefficiencies, and areas for improvement. Data analytics helps manufacturers optimise resource allocation, energy usage, and material costs.
By leveraging cloud computing and digital ecosystems, manufacturers can gain actionable insights to make informed decisions. Our article on AI-powered automation in engineering explores this in greater detail.
Digital Energy: A Critical Component of Asset Automation
Integrating digital energy solutions into asset automation can lead to substantial cost reductions in energy-intensive industries. Here’s how:
- Smart Grid Technology
With smart grid technology, manufacturers can efficiently manage energy consumption, reducing waste and lowering costs.
- Energy Management Systems (EMS)
Energy management systems allow businesses to monitor and optimise their energy usage in real time, ensuring sustainable practices and cost savings. For more, check out our guide to digital energy management systems.
- Renewable Energy Integration
Adopting renewable energy practices through asset automation not only reduces costs but also aligns with sustainable business objectives.
Key Technologies Driving Asset Automation
1. IoT Integration
The Industrial Internet of Things (IIoT) enables interconnected devices to communicate seamlessly, enhancing automation and control. By connecting machines, sensors, and systems, manufacturers can gather data to optimise operations.
2. SCADA and Process Control Systems
SCADA systems and process control systems offer centralised monitoring and control, ensuring that manufacturing processes run smoothly and efficiently.
3. Robotics and Automation Solutions
Integrating robotics into manufacturing processes improves precision, reduces waste, and minimises labour costs.
Discover how industrial automation solutions can transform your business in our dedicated guide.
Our Asset Automation Solutions
Benefits of Asset Automation for Manufacturers
- Cost Reductions
Asset automation plays a significant role in lowering operational expenses by optimising processes such as predictive maintenance and real-time monitoring. By detecting potential issues before they escalate into costly breakdowns and automating routine tasks, manufacturers can eliminate unnecessary repairs and reduce downtime, resulting in substantial cost savings over time. - Improved Productivity
Automation minimises human error and accelerates production cycles, ensuring consistent quality and maximised output. Systems such as process automation frameworks and SCADA systems streamline workflows, enabling operators to focus on strategic tasks while machines handle repetitive operations with unmatched precision and speed. - Enhanced Safety
Asset automation significantly improves workplace safety by integrating advanced technologies like safety instrumented systems (SIS) and predictive maintenance tools. These systems monitor critical equipment and processes in real-time, preventing hazardous failures, safeguarding workers, and reducing the risk of accidents in high-risk industrial environments. - Sustainability
Automation supports eco-friendly practices by enabling energy-efficient technologies and minimising resource waste. Through precise control of machinery and the integration of energy management systems (EMS), manufacturers can significantly reduce their carbon footprint while maintaining high levels of operational efficiency. - Scalability
Modern automation solutions are designed to be flexible and scalable, allowing manufacturers to easily expand operations to meet increased demand or incorporate new projects. Whether adding production lines, upgrading to IoT-enabled devices, or implementing cloud-based automation platforms, scaling becomes seamless and cost-effective with asset automation.
Case Studies: How Asset Automation Transformed Business Operations
At 4Sight OT | Automation, we believe in the power of real-world examples to illustrate the effectiveness of our solutions. Our case studies showcase how we have successfully implemented asset automation and predictive maintenance strategies across various industries, delivering tangible results for our clients.
- AFGRI Animal Feeds SCADA, PLC & MCC: Discover how we enhanced operational efficiency through advanced automation technologies.
- 4Sight AGE Secures R40 Million Project with Zimplats: Learn about our strategic partnership that led to a significant project win, demonstrating our expertise in automation and digital transformation.
- Carbon Plant Upgrade for Ingrain: Explore how we modernised production capabilities through a comprehensive upgrade of automation systems.
We invite you to delve into these case studies to see firsthand how 4Sight OT | Automation can help your organisation achieve operational excellence through innovative automation solutions.
Overcoming Challenges in Asset Automation
While asset automation offers immense benefits, implementation can present challenges, such as:
- Initial Costs: Investments in hardware, software, and training may be substantial.
- Change Management: Employees must adapt to new systems and workflows.
- Cybersecurity: Protecting industrial control systems against cyber threats is critical.
At 4Sight OT Automation, we provide tailored solutions to address these challenges, ensuring a seamless transition to automated systems.
The State of Asset Automation in South Africa
South Africa is rapidly embracing asset automation to drive innovation, enhance productivity, and remain competitive in the global market. Industries such as mining, manufacturing, and energy are leading the adoption of advanced automation technologies to address unique challenges and unlock new opportunities.
1. Widespread Adoption Across Industries
Sectors like mining and manufacturing, which are cornerstones of the South African economy, are increasingly leveraging automation and control systems to optimise operations. From predictive maintenance tools in mining equipment to robotics process automation (RPA) in assembly lines, businesses are adopting solutions that improve efficiency while cutting costs.
2. Challenges Hindering Full Implementation
Despite the significant strides, the adoption of asset automation faces some hurdles, including high initial investment costs and the need for skilled labour to operate and maintain these systems. In addition, the availability of reliable infrastructure, such as stable energy and robust connectivity for IIoT integration, remains a challenge in some regions.
3. Government and Private Sector Collaboration
To address these barriers, South African businesses and government agencies are collaborating to promote the digital transformation of industries. Initiatives to support Industry 4.0 adoption and provide incentives for automation investments are fostering an environment where innovation can thrive.
4. A Promising Outlook
With advancements in technologies like SCADA systems, cloud computing, and energy management systems, the future of asset automation in South Africa is bright. Companies are recognising the potential for improved productivity, cost reductions, and enhanced sustainability, setting the stage for a more competitive and technology-driven industrial landscape.
As a leading provider, 4Sight OT Automation continues to empower businesses across South Africa with cutting-edge automation solutions that meet the region's dynamic needs.
Future Trends in Asset Automation
The future of asset automation is brimming with transformative innovations, pushing the boundaries of efficiency, sustainability, and technological integration. Here’s a closer look at the most impactful trends shaping the industry:
1. Artificial Intelligence
Artificial Intelligence (AI) is redefining how manufacturers approach predictive maintenance and process optimisation. Advanced AI algorithms analyse massive datasets collected from smart assets and sensors to identify patterns, predict equipment failures, and recommend maintenance schedules.
- Enhanced Predictive Maintenance: AI tools can forecast issues with greater accuracy, reducing downtime and unexpected breakdowns. For instance, machine learning models can predict when a motor bearing will wear out based on vibration analysis.
- Process Optimisation: AI-driven systems dynamically adjust production processes to optimise energy usage, improve quality, and minimise waste. This not only reduces operational costs but also ensures consistent output even in complex manufacturing environments.
As AI technology continues to evolve, its integration with robotics process automation (RPA) and industrial Internet of Things (IIoT) will revolutionise operational capabilities.
2. Cloud Integration
The shift to cloud-based solutions is making automation platforms more scalable, flexible, and accessible. Instead of relying on localised infrastructure, manufacturers are increasingly adopting cloud technologies to centralise data, enable remote monitoring, and enhance collaboration.
- Scalable Platforms: Cloud-based automation systems grow with your needs, whether it’s adding new production lines or integrating additional monitoring systems.
- Cost-Effective Deployment: By eliminating the need for expensive on-site servers, cloud solutions reduce capital expenditure and streamline maintenance costs.
- Data Accessibility: Real-time data can be accessed and analysed from anywhere, empowering decision-makers with the insights needed to act swiftly.
Cloud integration also supports disaster recovery and ensures system redundancy, providing a robust backbone for modern manufacturing processes.
3. Digital Twins
A digital twin is a virtual representation of a physical asset, enabling manufacturers to simulate, test, and optimise equipment and processes in a risk-free digital environment.
- Advanced Simulations: Digital twins allow for detailed modelling of systems, helping engineers identify inefficiencies and explore performance improvements without disrupting operations.
- Proactive Maintenance: By comparing real-time data from physical assets with their digital counterparts, manufacturers can detect anomalies and predict failures with pinpoint accuracy.
- Training and Development: Virtual replicas serve as effective training tools, allowing teams to practice system operations, maintenance tasks, or troubleshooting scenarios without impacting the actual equipment.
With advancements in augmented reality (AR) and virtual reality (VR), digital twins will become even more interactive and intuitive.
4. Sustainable Practices
The global push towards sustainability is influencing every aspect of manufacturing, and asset automation is playing a pivotal role in supporting eco-friendly operations.
- Energy-Efficient Technologies: Automation systems integrated with smart grid technology and energy management systems (EMS) optimise energy usage, reducing waste and cutting costs.
- Reduced Carbon Footprint: Asset automation solutions help minimise resource consumption, enabling manufacturers to meet environmental compliance standards while lowering their carbon footprint.
- Circular Manufacturing: By leveraging technologies like IoT integration and asset lifecycle management, businesses can extend the lifespan of machinery and implement recycling processes for unused resources or outdated equipment.
These sustainable practices align with the broader goals of Industry 4.0, ensuring that manufacturers remain competitive while contributing positively to environmental preservation.
The convergence of AI, cloud integration, digital twins, and sustainability within asset automation is reshaping the manufacturing landscape. Companies that embrace these trends will not only achieve superior efficiency but also future-proof their operations in an increasingly dynamic industrial environment. As a leader in automation solutions, 4Sight OT Automation stands ready to help businesses leverage these cutting-edge advancements for success.
Internal and External Links to Support Learning
For more insights, explore our articles on:
Partner with 4Sight for your Asset Automation
Asset automation is more than a technological advancement—it’s a strategy that drives significant cost savings and operational excellence in manufacturing. By incorporating smart assets, predictive maintenance, and digital energy solutions, manufacturers can unlock unprecedented efficiencies and remain competitive.
At 4Sight OT Automation, we are committed to delivering cutting-edge asset automation solutions tailored to your unique needs. Contact us to learn how we can revolutionise your manufacturing processes.