Offerings
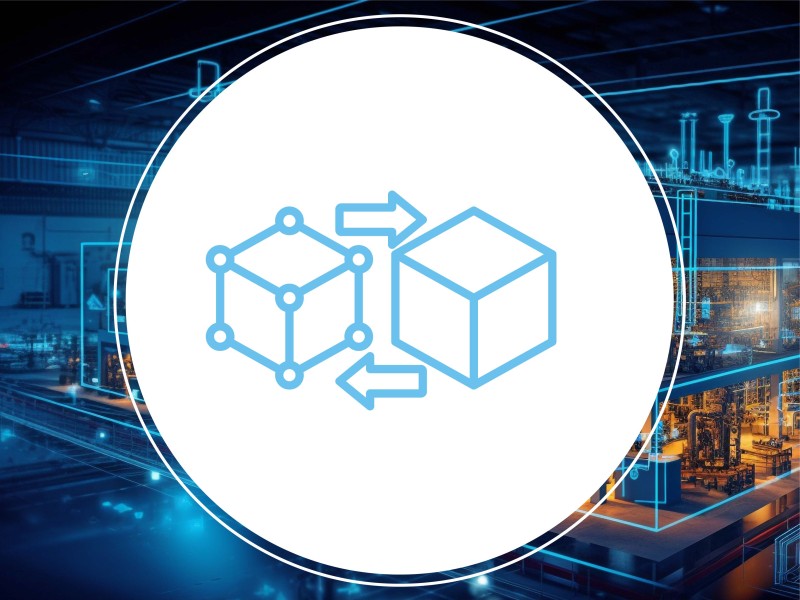
Digital Twin Technology
Transforming Operations with Real-Time Insights and Predictive Modelling
Digital Twin Technology creates a virtual replica of physical assets, processes, or systems used in industry operations. This technology allows companies to simulate, monitor, and optimise real-world operations by providing real-time data insights. By modelling industrial equipment and processes, digital twins help predict outcomes, identify inefficiencies, and improve performance without disrupting actual operations. They enable better decision-making, reduce downtime, and enhance productivity across industries.
How AI-Enhanced Digital Twin Technology helps companies
Companies are leveraging AI-embedded digital twin technology to embark on their journey into the industrial metaverse, accurately modelling industrial equipment and processes. The benefits of creating simulations within AI-enhanced digital twin software are manifold, often surpassing the initial costs of model creation. These digital twins enable meticulous monitoring of assets and processes, offering insights into improving efficiency. The integration of AI illuminates inefficiencies that might otherwise remain obscured, particularly in complex production processes spanning vast areas. For instance, in industries such as refining, where facilities cover multiple city blocks, AI-powered digital twin software provides a comprehensive overview that would be impossible for a single observer. Furthermore, AI-embedded digital twin technology empowers plant operators and process engineers to conduct experiments and accurately predict production outcomes. Notably, if adjustments to operating parameters in the simulation lead to asset failure, the digital model can be instantly reverted to a previous state, allowing operators to fine-tune conditions without risking physical assets or causing costly production disruptions.
From design concept into operations, the Digital Twin keeps delivering benefits.
- Conceptual design: Optimise complex design processes by simulating layouts, configurations, operating conditions, and risk scenarios.
- Front-end engineering and design: Create a living repository for engineering data to identify potential clashes, optimize resources and construction, and facilitate continual handover.
- Detailed Design: Give all stakeholders visibility into the design process, set deliverable expectations, and ensure seamless handover, which reduces onsite activity and improves collaboration–between operators or amongst multiple vendors.
- Procurement: Reduce lead time by integrating procurement planning into the design process. Cross-reference design documentation
with procurement and commissioning to increase transparency. - Construction: Link design, procurement, and construction processes to enable parallel activities. Create virtual replicas of construction sites to identify potential issues, optimize resources, reduce rework, and improve construction timelines.
- Commissioning: Use digital documentation and deliverables to speed up commissioning and ensure a smooth handover to operations.
- Operations: Leverage engineering data in operations to increase safety, sustainability, and agility while reducing costs. Ensure ongoing partnership between 4Sight and operators through engineering data maintenance or equipment refinements.
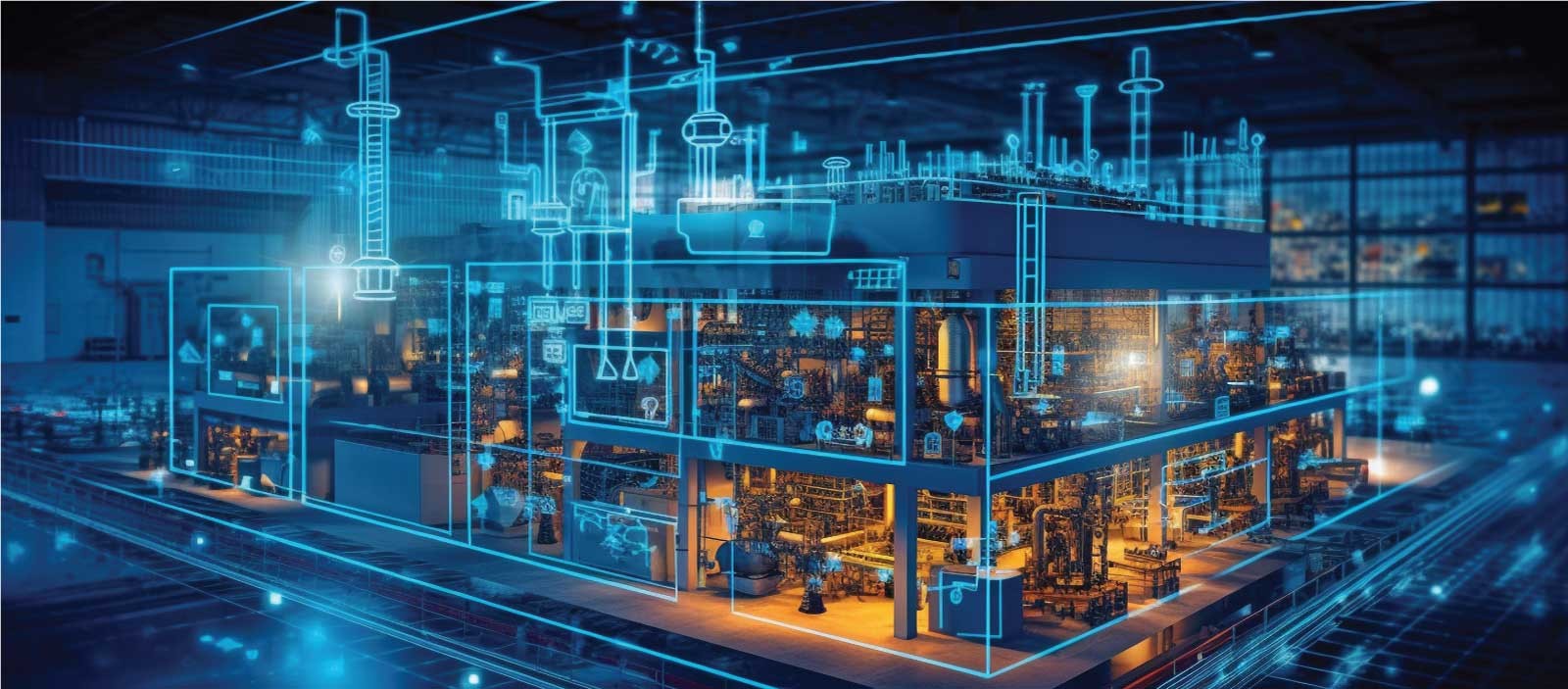
Digital Twin Technology puts sustainability targets within reach
Our extensive expertise in simulation technology provides you with unparalleled insights into complex systems, enabling the identification and resolution of both current inefficiencies and future challenges. By utilising simulation solutions, we offer a low-risk approach to driving transformative change. Our authentic digital twin model encapsulates all constraints, business rules, and decision logic influencing the functionality of your system. Leveraging your data, we seamlessly evaluate numerous scenarios and deliver optimised solutions. Regardless of your industry, our proficiency in digital twin technology ensures the elimination of even your most challenging operational and process scheduling obstacles.
Moreover, by simulating various scenarios and optimising processes, we assist companies in progressing towards their net-zero targets, contributing to a sustainable future. Digital twins enable real-time monitoring of the carbon footprint throughout the entire supply chain, accurately calculating carbon emissions at every stage of product design and development. This capability ensures a transparent and sustainable journey from design through to delivery.
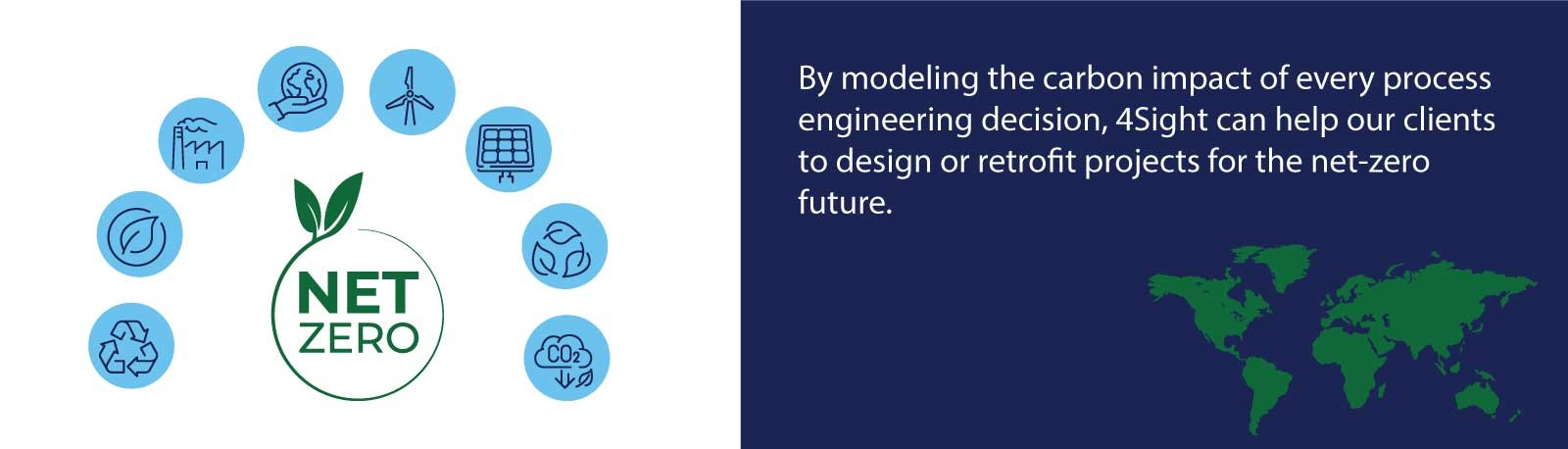
4Sight OT Simulation possesses extensive knowledge and expertise in AI-driven Digital Twin Technologies, backed by years of experience in the mining and manufacturing sectors. Our team leverages cutting-edge AI solutions to create sophisticated digital twin models that enhance operational efficiency and decision-making. By integrating advanced simulation techniques with industry-specific insights, we empower businesses to optimise their processes, reduce downtime, and drive transformative change in their operations.
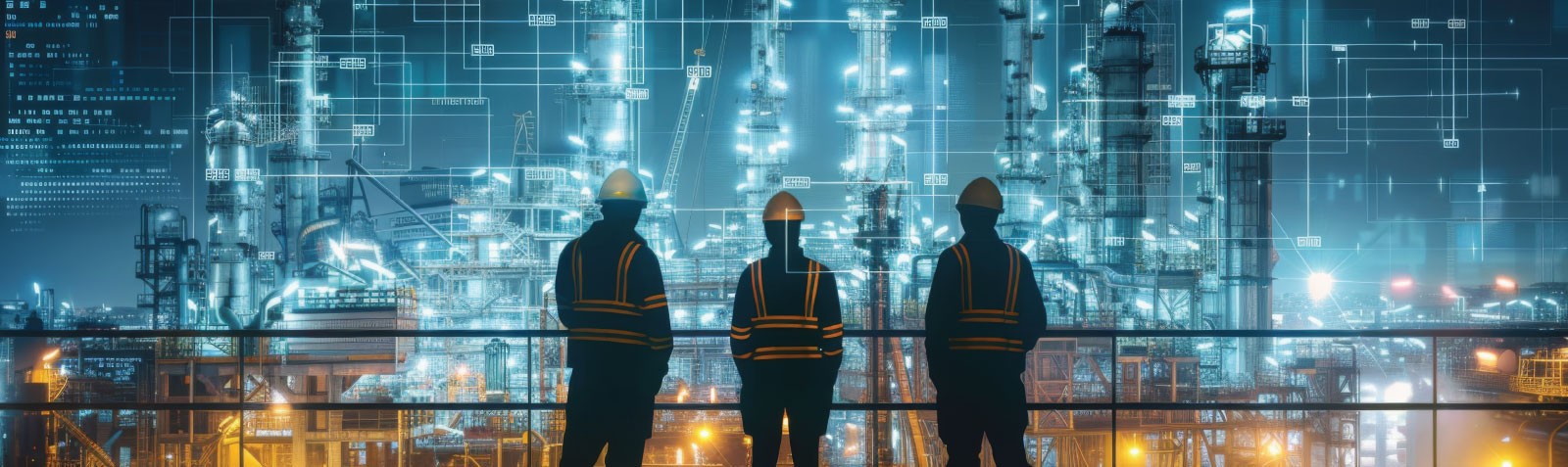