Power and Energy Monitoring in Manufacturing - 4Sight
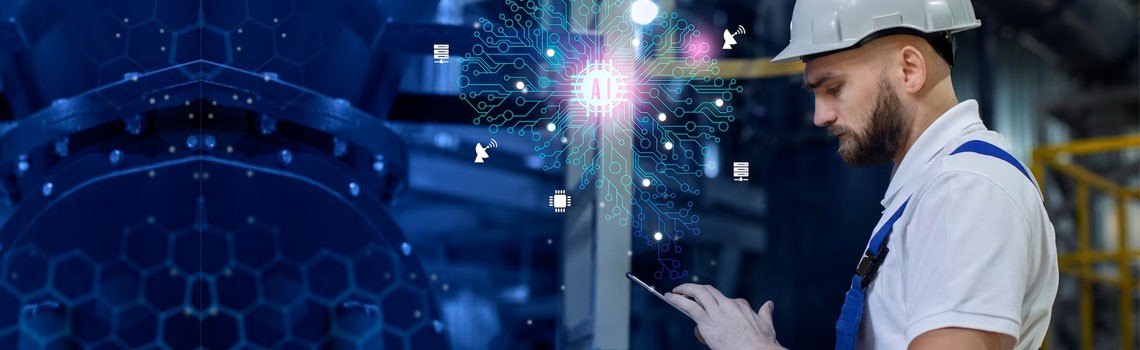
4Sight OT Automation provides Digital Solutions for Power and Energy Monitoring and Management in Manufacturing industries and plants. Our Digital Energy solutions are focussed on Enhancing Business and Operational Efficiency: Discover the Benefits of 4Sight's Digital solutions for Power and Energy Monitoring in Manufacturing, and get our team onboard for solutions that will take your manufacturing plant to the next level.
Empowering Manufacturing Excellence: 4Sight OT Automation's Digital Energy Solutions for Power and Energy Monitoring in Manufacturing
In the dynamic landscape of manufacturing, the quest for operational excellence is an ongoing journey. One critical aspect that plays a pivotal role in achieving this goal is the effectiveness of Power and Energy Monitoring in Manufacturing. 4Sight OT Automation stands at the forefront of this endeavour, offering cutting-edge Digital Energy Solutions designed to empower manufacturers with deep insights, informed decision-making, and a host of operational benefits.
Digital Energy: A Paradigm Shift for the Manufacturing Industry
4Sight OT Automation's digital solutions for Power and Energy Monitoring in Manufacturing represent a paradigm shift in the way manufacturers approach energy management. These solutions leverage digital technologies to enhance energy efficiency, reduce costs, improve reliability, and support sustainability goals. Encompassing various energy types, including electricity, gas, water, air, and steam, Digital Energy serves as a comprehensive platform for ushering in a new era of smart and sustainable Power and Energy Monitoring in Manufacturing.
Energy Management Excellence
At the heart of 4Sight OT Automation's Digital Energy solutions for Power and Energy Monitoring in Manufacturing, lies the commitment to excellence in energy management. The tools and platforms provided empower users to monitor, analyse, and optimise energy usage across different systems and processes. This includes the identification of energy-saving opportunities, the implementation of demand response strategies, and the efficient management of energy resources.
Power Monitoring and Management
Real-time monitoring of the electrical infrastructure health and power consumption is a cornerstone of 4Sight OT Automation's Digital Energy solutions for Power and Energy Monitoring in Manufacturing. This capability allows businesses to proactively manage their electrical systems, identifying issues, optimising power usage, and ultimately enhancing the overall reliability and performance of their electrical infrastructure.
Microgrids and Distributed Energy Resources (DER) Management
As the global push toward renewable energy intensifies, manufacturers are increasingly integrating decentralised energy resources into their operations. 4Sight OT Automation's Digital Energy solutions for Power and Energy Monitoring in Manufacturing excel in facilitating the seamless integration and management of microgrids, solar panels, wind turbines, energy storage systems, and other DERs. By actively controlling and optimising these resources, businesses can maximise power availability, reduce cost through effective selection of available resources, reduce grid dependency, and enhance overall energy resilience.
Power Quality Mitigation
Power Quality incidents may cause significant downtime in manufacturing and loss of revenue. Identifying and addressing power quality concerns is a critical component of 4Sight OT Automation's Digital Energy solutions for Power and Energy Monitoring in Manufacturing. The platform provides effective solutions, including passive and active power factor correction, active harmonic mitigation, voltage regulation, and dip mitigation. These measures empower businesses to proactively address power-related issues, ensuring optimal system performance and minimising the risk of disruptions.
Ongoing Monitoring for Peak Efficiency
4Sight OT Automation recognises that the journey toward manufacturing excellence is an ongoing process. To gauge the effectiveness of interventions and ensure sustained benefits, ongoing monitoring is crucial. The platform enables continuous monitoring, allowing businesses to verify achieved benefits and make informed adjustments to keep systems operating at peak efficiency.
Benefits of 4Sight OT Automation's Digital Solutions for Power and Energy Monitoring in Manufacturing:
1. Enhanced Safety and Availability:
- Risk Mitigation: Proactive monitoring of energy resources in Manufacturing allows businesses to identify potential hazards and risks promptly. Early detection of anomalies in power quality and consumption minimises the likelihood of equipment failures that could compromise safety.
- Downtime Reduction: Efficient management of energy resources reduces the risk of unplanned downtime, ensuring continuous operations and production.
- Operational Continuity: By ensuring the availability of energy resources, Digital Energy solutions for Power and Energy Monitoring in Manufacturing contribute to maintaining operational continuity even in the face of unforeseen challenges.
2. Operational Efficiency Redefined:
- Resource Optimisation: In-depth analysis of energy usage allows businesses to optimise resource allocation, ensuring that energy is utilised efficiently across different processes and systems.
- Process Streamlining: Identification of energy-saving opportunities enables streamlining of manufacturing processes, reducing waste and enhancing overall operational efficiency.
- Increased Productivity: Efficient Power and Energy Monitoring in Manufacturing translates into a more streamlined production process, increasing overall productivity and output.
3. Cost Reductions on a Scale:
- Energy Consumption Insights: Digital Energy solutions for Power and Energy Monitoring in Manufacturing provide granular insights into energy consumption patterns, allowing manufacturing plants to identify areas where energy costs can be reduced.
- Demand Response Strategies: Implementation of demand response strategies based on real-time monitoring helps in optimising energy usage during peak demand periods, reducing overall energy costs.
- Operational Cost Savings: Reduced energy consumption and optimised processes contribute to significant operational cost savings over time.
4. Elevated Equipment Reliability:
- Preventive Maintenance: Proactive power quality mitigation measures contribute to preventive maintenance, reducing the risk of unexpected equipment failures and extending the lifespan of critical assets.
- Equipment Performance Optimisation: Continuous monitoring allows businesses to optimise equipment performance, ensuring that machinery operates within optimal parameters.
- Reduced Downtime: Ensuring the reliability of equipment contributes to reduced downtime, as the risk of unplanned outages due to equipment failure is minimised.
5. Aligned with Sustainability Goals:
- Renewable Energy Maximisation: Integration and optimisation of decentralised energy resources contribute to the maximisation of renewable energy usage, aligning with sustainability objectives.
- Environmental Footprint Reduction: Adoption of energy-efficient practices and reliance on renewable energy sources contribute to a reduction in the environmental footprint of manufacturing operations.
- Corporate Social Responsibility (CSR): Meeting sustainability goals enhances the company's CSR profile, demonstrating a commitment to environmental stewardship and responsible business practices.
Digital Solutions for Power and Energy Monitoring in Manufacturing - A game-changer for Manufacturers in South Africa
In conclusion, 4Sight OT Automation's Digital Energy solutions are a game-changer for manufacturers in South Africa seeking to excel in the competitive landscape of modern industry. By harnessing the power of digital technologies, these solutions for Power and Energy Monitoring in Manufacturing provide a comprehensive platform, enabling businesses to make informed decisions, improve operational efficiency, and achieve their sustainability goals. As manufacturing continues to evolve, the role of Digital Energy in shaping a more resilient, efficient, and sustainable future becomes increasingly evident. With 4Sight OT Automation, the journey toward manufacturing excellence is powered by innovation and guided by a commitment to delivering transformative solutions for Power and Energy Monitoring in Manufacturing, and the challenges of today and tomorrow.
Frequently Asked Questions about 4Sight's Digital Solutions for Power and Energy Monitoring in Manufacturing
- What does 4Sight's Digital Power and Energy Monitoring solution offer for manufacturing facilities?
Our solution provides a comprehensive platform using advanced sensors and analytics to monitor, analyse, and optimise power and energy usage in manufacturing processes. - How can 4Sight's solution help manufacturing facilities reduce energy costs?
By offering real-time insights and analytics, our solution identifies energy inefficiencies, enabling manufacturing facilities to implement strategies that reduce energy consumption and lower operational costs. - Can the Digital Power and Energy Monitoring solution be tailored to different manufacturing processes?
Yes, our solution is highly customisable to accommodate the unique energy requirements of diverse manufacturing processes, ensuring optimal efficiency. - What role does predictive maintenance play in the context of power and energy monitoring for manufacturing?
Predictive maintenance forecasts potential equipment failures, minimising downtime and ensuring the continuous operation of manufacturing processes. - How does 4Sight's solution contribute to sustainability in manufacturing?
By monitoring and optimising energy usage, our solution aligns manufacturing processes with sustainability goals, reducing carbon footprint and promoting eco-friendly practices. - Is it possible to integrate 4Sight's Digital Power and Energy Monitoring solution with existing manufacturing systems?
Yes, our solution is designed for seamless integration with existing manufacturing systems, minimising disruption and ensuring compatibility. - Can 4Sight's solution adapt to changes in production volumes and manufacturing schedules?
Absolutely, our solution utilises automation and adaptive algorithms to adjust to variations in production volumes and schedules, optimising energy usage accordingly. - How does 4Sight's solution support compliance with energy regulations in the manufacturing sector?
Our solution provides real-time data and reporting features that facilitate compliance with energy regulations, ensuring manufacturing facilities meet industry standards. - Is specialised training required for manufacturing personnel to use 4Sight's Digital Power and Energy Monitoring solution?
While our solution is user-friendly, we recommend basic training to empower manufacturing personnel to leverage the full potential of the system. - Can 4Sight's solution help manufacturing facilities participate in energy incentive programs?
Yes, our solution supports participation in energy incentive programs by optimising energy usage and contributing to overall energy conservation efforts. - What measurable benefits can a manufacturing facility expect from implementing 4Sight's solution?
Implementing our solution can lead to significant cost savings, reduced downtime, enhanced sustainability, improved regulatory compliance, and increased operational efficiency for manufacturing facilities. - How does 4Sight's solution assist in identifying energy-intensive processes within a manufacturing facility?
Our solution provides detailed analytics that pinpoint energy-intensive processes, allowing manufacturing facilities to prioritise optimisation efforts. - Can 4Sight's solution help manufacturers track and reduce peak demand charges?
Yes, our solution offers insights into peak demand periods, enabling manufacturers to implement strategies that minimise peak demand charges. - Does 4Sight's solution provide historical data for trend analysis in energy usage?
Absolutely, our solution offers comprehensive historical data, empowering manufacturing facilities to analyse trends and make informed decisions for continuous improvement. - How does 4Sight's solution contribute to the overall efficiency of manufacturing processes?
By optimising power and energy usage, our solution enhances overall operational efficiency in manufacturing, leading to improved productivity and reduced waste.