The Benefits of Electric Mine Simulation
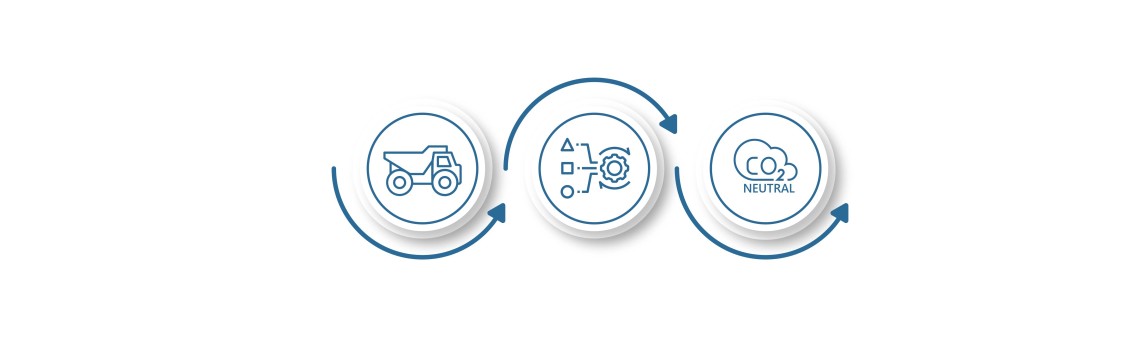
Simulation is the key to understanding the impacts of electrification on mine operations.
Electrification is the solution that hits economic, environmental, and health goals – this means that once it reaches a tipping point, the transition will accelerate. The road to zero emissions requires vehicles and machinery powered by renewable energy. Mining simulations making use of battery electric vehicles (BEV’s) that interface with Electrical supply and consumption simulations allow mining companies to optimise their electric mine fleet by analysing and testing various scenarios and identifying the most efficient ways to deploy the solution.
Groundbreaking collaboration between 4Sight and SimGenics, a comprehensive simulation solution designed to revolutionise the mining industry. With a shared commitment to sustainability and efficiency, our integrated platform offers a full-scope simulation approach that delivers unparalleled insights into the cost and carbon footprint impact throughout a mine's entire life cycle. By harnessing advanced modeling techniques and cutting-edge technologies, our solution empowers mining companies to make informed decisions that optimise operations, reduce environmental impact, and maximise profitability. With clear and integrated results at your fingertips, you can make informed decisions on the carbon footprint impact over the life cycle of your mining operation.
4Sight and SimGenics uses SimMine® to simulate the mine’s electrical fleet that allows testing of various options to reduce carbon footprint, including:
- Reduce Risk: Shifting from a fossil fuel powered mine to an entirely electrically powered mine is a whole-of-systems shift from one energy technology to another. It is a challenge that has yet to be attempted in mining at the pace required.
- Mine Fleet: Comparing fossil fuel-powered, hybrid, and BEV’s for development, ramp-up and steady-state production, including details like variable speeds, fuel consumption and power consumption/regeneration per vehicle type, depending on payload and mine gradients. Scenario analysis to optimize dynamic fleet sizing.
- Charging Stations Strategies:
- Determine the optimal location and the number of charging stations required for the life of mine.
- Operating philosophies; battery swap vs. fast charging
- Improved Efficiency: Simulation allows mining companies to optimise their electric mine vehicle utilisation by comparing various scenarios and identifying the option with the highest performance. This illustrates the potential to reduce energy consumption and minimize carbon emissions.
- Reduced Operating Costs: Simulation can help mining companies identify areas where they can reduce operating costs through optimising routes and schedules of BEV’s.
- Design Optimisation: The solution fully integrates with most Mine Design software packages, enabling rapid modelling of new or existing mines based on the mine design and mining method, providing outputs showing:
- Mine design (layout) constraints
- Potential layout optimisation options
- Recharging infrastructure location and capacity requirements
- Potential development constraints and options to alleviate them.
- Rock handling systems: Simulation includes rock handling of development and LOM Production from in-situ rock to surface, showing:
- Buffer Capacity Requirements to alleviate potential bottlenecks.
- Considerations of energy supply since the rock handling system is a significant power consumer.
- Control logic used to regulate the system’s behavior, e.g., ventilation considerations, power grid capacity, etc.
- Environmental Impact Electrification is central to the decarbonisation journey. It is the medium for consuming, transferring and optimising renewable energy. It also assists mines in meeting regulatory requirements and attracting environmentally conscious customers.
In summary, electric mine vehicle simulations can provide mining companies a cost-effective and efficient way to reduce their carbon footprint while analysing their operations and production targets.
A full scope solution
- Existing simulation platforms limited to solving models in Event-Based / Continuous fashion resulting in limitations in the scope of mine processes that can be simulated accurately, and the insights offered by the results.
- This is particularly a problem when comparing the full scope of a diesel vs electric mine, since both Event-Based and Continuous models need to be solved synchronously to produce accurate results over LOM to reduce risks.
- The integrated mine simulation solves Event-Based and Continuous models as a single synchronized model, producing highly accurate, day-to-day results for optimal schedules, costing and carbon footprint monitoring of an electric, hybrid or diesel version of a mine, or a combination thereof.
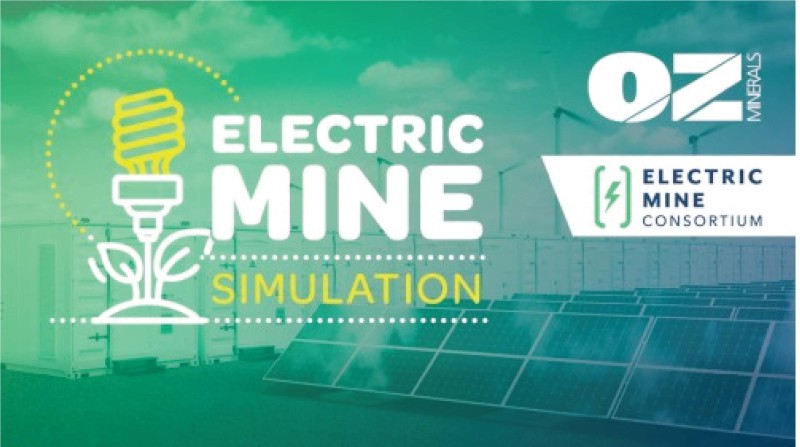
Did you know? 4Sight has been chosen for the electric mine simulation project aiming for a zero-carbon future
4Sight’s Asset Simulation team, represented by its subsidiary Simulation Engineering Technologies (SET), has been chosen as one of two South African companies to run simulation projects at Australian Mining Company OZ Minerals’ Prominent Hill Mine. These projects are aimed at testing how simulation can help executives understand the impact of electrification on mine design and production, infrastructure and energy management. 4Sight’s Asset Simulation is now working to create a platform for developing and testing various layouts for the electrification of Prominent Hill’s mining operations.