The Impact of Asset Automation on Predictive Maintenance
Find out how predictive maintenance powered by asset automation is reshaping industries, boosting efficiency, and ensuring sustainable operations.
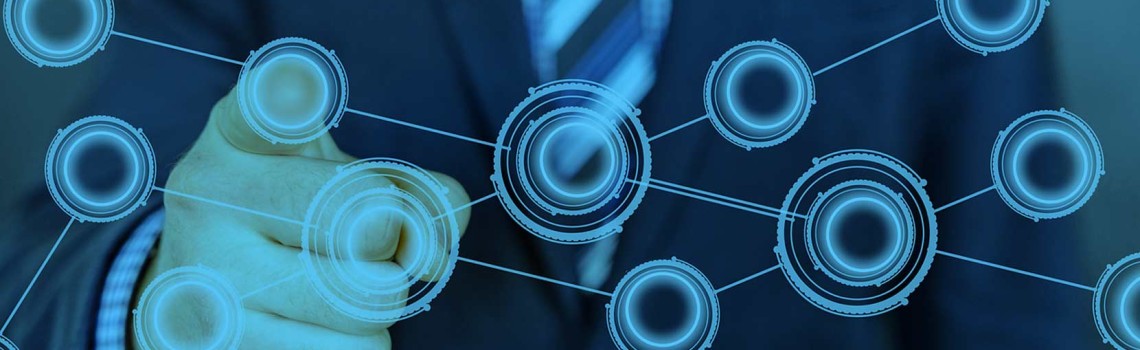
Find out how predictive maintenance powered by asset automation is reshaping industries, boosting efficiency, and ensuring sustainable operations.
What Is Predictive Maintenance?
Predictive maintenance is a proactive approach to managing equipment and assets, aiming to foresee and address potential issues before they lead to downtime. It relies on advanced technologies, such as sensors, data analytics, and machine learning, to monitor the condition of machinery in real time.
Traditional Maintenance Strategies
Before the rise of predictive maintenance, industries primarily relied on two approaches:
- Reactive Maintenance: Fixing equipment after a breakdown occurs. This method often results in significant downtime and high repair costs.
- Preventive Maintenance: Scheduled servicing based on fixed time intervals, regardless of the actual condition of the equipment. While better than reactive methods, it may lead to unnecessary servicing or missed signs of impending failure.
Predictive maintenance offers a smarter alternative, reducing costs and improving operational efficiency.
The Role of Asset Automation
Overview of Asset Automation Technologies
Asset automation is revolutionising industrial processes by integrating sophisticated technologies that deliver efficiency, accuracy, and scalability. Systems like SCADA (Supervisory Control and Data Acquisition), PLC programming (Programmable Logic Controllers), and MCCs (Motor Control Centres) form the backbone of asset automation.
- SCADA Systems: SCADA enables real-time monitoring and control of processes across diverse industrial environments. By providing a centralised interface, operators can track equipment performance, identify inefficiencies, and address issues promptly.
- PLC Programming: PLCs are essential for automating machinery and processes. These controllers are highly adaptable, allowing businesses to implement tailored automation solutions that suit their specific requirements.
- MCCs: Motor Control Centres manage and control the electrical systems of motors, ensuring operational reliability while providing safeguards against electrical faults.
By combining these technologies with advanced monitoring tools, asset automation systems enable continuous data acquisition and processing. The result? Improved maintenance, optimised operations, and reduced downtime.
Integration with Predictive Maintenance
Predictive maintenance and asset automation go hand in hand, transforming how industries manage their critical assets. Asset automation enables seamless integration with predictive maintenance strategies through:
- IoT Sensors: Sensors embedded within machinery collect real-time data, tracking parameters like temperature, vibration, and operational loads. This granular monitoring allows for early detection of anomalies.
- Machine Learning Algorithms: By analysing data patterns, machine learning identifies potential failures and forecasts maintenance needs with remarkable precision. These algorithms learn over time, continually improving their accuracy.
- Automated Alerts and Actions: Asset automation systems trigger automatic alerts when parameters deviate from safe ranges. They can also initiate predefined actions, such as shutting down equipment to prevent damage or deploying repair protocols.
These capabilities not only enhance predictive maintenance but also create a robust foundation for long-term asset management. To explore more about industrial automation and its benefits, visit this guide on automation companies in South Africa.
Benefits of Combining Automation with Predictive Maintenance
Increased Operational Efficiency
By integrating automation technologies like Distributed Control Systems (DCS) and Energy Management Systems (EMS), businesses can achieve seamless operations with minimal manual intervention. These systems centralise control and automate processes, ensuring optimal performance of industrial equipment.
- DCS: Distributed Control Systems enable efficient coordination of multiple processes within a plant. By automating complex operations and providing real-time feedback, they help operators focus on higher-value tasks rather than routine monitoring.
- EMS: Energy Management Systems track and optimise energy usage across facilities, ensuring resources are used efficiently without compromising productivity.
The result is a significant boost in operational efficiency, with faster response times, reduced errors, and streamlined workflows.
Reduction in Unplanned Downtime
Unplanned downtime is one of the most costly challenges faced by industries. By combining asset automation with predictive maintenance, organisations can drastically reduce unexpected failures.
- Proactive Issue Detection: IoT sensors monitor equipment health continuously, detecting deviations from normal operational parameters before they escalate.
- Automated Maintenance Scheduling: Machine learning algorithms assess data trends to predict maintenance needs, enabling timely interventions.
- Reduced Dependence on Reactive Repairs: Instead of waiting for breakdowns, automated systems ensure repairs are planned and executed without disrupting production.
These measures minimise disruptions, extend asset life, and improve overall productivity.
Enhanced Accuracy in Failure Predictions
Accurate predictions are the cornerstone of effective maintenance strategies. Tools such as real-time monitoring systems and predictive maintenance software are pivotal in refining failure forecasts.
- Real-Time Monitoring: Advanced sensors capture high-resolution data, from vibration patterns to temperature changes, ensuring that even minor irregularities are detected.
- Predictive Analytics: Algorithms analyse historical and current data to identify patterns that signal potential failures. These insights allow organisations to act with confidence, addressing issues before they escalate.
- Data-Driven Decision Making: With precise failure predictions, businesses can allocate resources more effectively, prioritising maintenance tasks that have the greatest impact on operational continuity.
For a deeper understanding of quality control in automation systems, visit this resource.
By leveraging automation with predictive maintenance, organisations not only enhance their maintenance strategies but also create a more reliable, efficient, and future-ready operational framework.
Key Technologies Driving Asset Automation
IoT Sensors and Data Collection
Internet of Things (IoT) sensors play a crucial role in gathering real-time data on equipment performance, temperature, pressure, and other critical parameters.
Machine Learning Algorithms
Machine learning enhances predictive analytics by identifying complex patterns and anomalies that signal potential issues.
Cloud Computing
Cloud platforms enable efficient data processing and storage, providing scalability and accessibility across global operations.
Explore how AI-powered automation is revolutionising engineering by visiting this link.
Real-World Applications of Automated Predictive Maintenance
Manufacturing Industry
In manufacturing, asset automation enables proactive maintenance of machinery, reducing production delays and enhancing product quality.
Energy Sector
With digital energy management systems, power plants and renewable energy facilities monitor equipment health and optimise energy distribution, ensuring uninterrupted service.
Mining Operations
Mining companies use automation systems like SCADA and PLC programming to monitor heavy machinery, preventing costly breakdowns.
Read more about electrical and instrumentation solutions at 4Sight Asset Automation.
Challenges and Considerations
Barriers to Implementation
While the benefits are clear, challenges such as high initial costs and the need for specialised skills can hinder adoption.
Data Security and Privacy Concerns
As systems become more connected, ensuring robust cybersecurity measures is essential to protect sensitive operational data. For more on the importance of digitisation and automation in predictive maintenance, visit this external source.
Future Trends in Predictive Maintenance and Automation
Emerging Technologies
Advancements in Artificial Intelligence (AI) and Industrial Internet of Things (IIoT) are expected to further enhance the capabilities of predictive maintenance systems.
Market Growth
The predictive maintenance market is set to grow exponentially, driven by increasing demand for efficient asset management and reduced downtime.
For insights into digital energy management systems, check out this resource.
Why Choose 4Sight OT Automation?
4Sight OT Automation, formerly known as AGE Technologies, is a trusted leader in asset automation and control systems. With years of expertise and a proven track record, 4Sight stands out as a partner of choice for organisations seeking to implement predictive maintenance solutions.
Expertise Across Industries
4Sight offers tailored solutions designed to meet the unique challenges of industries such as manufacturing, mining, energy, and logistics. Their systems are powered by cutting-edge technologies, including:
- Motor Control Centres (MCCs): For efficient motor management and fault protection.
- Control System Integration: Delivering seamless integration between hardware and software for streamlined operations.
- Safety Instrumented Systems (SIS): Ensuring safety and compliance in critical industrial processes.
Comprehensive Solutions for a Future-Ready Business
Whether it's optimising energy use with Energy Management Systems (EMS) or improving equipment monitoring with SCADA, 4Sight's solutions empower businesses to:
- Reduce downtime and maintenance costs.
- Extend the lifespan of critical assets.
- Stay ahead in competitive markets through advanced automation.
Commitment to Innovation and Support
What sets 4Sight apart is its dedication to innovation and exceptional customer support. By investing in the latest technologies and providing end-to-end implementation services, 4Sight ensures its clients remain efficient, secure, and ready for future challenges.
Choose 4Sight OT Automation for your predictive maintenance and automation needs, and experience the difference of working with an industry leader. For more information, explore 4Sight Asset Automation's services.
Revolutionise your maintenance strategies with 4Sight OT Automation
Our cutting-edge solutions in asset automation empower businesses to minimise downtime, reduce costs, and maximise asset lifespan.
Discover more about our services today:
- Industrial Automation Companies in South Africa
- AI-Powered Automation in Engineering
- Electrical and Instrumentation Companies
Let us help you stay ahead in the rapidly evolving industrial landscape. Contact us now to start your journey toward predictive maintenance excellence.